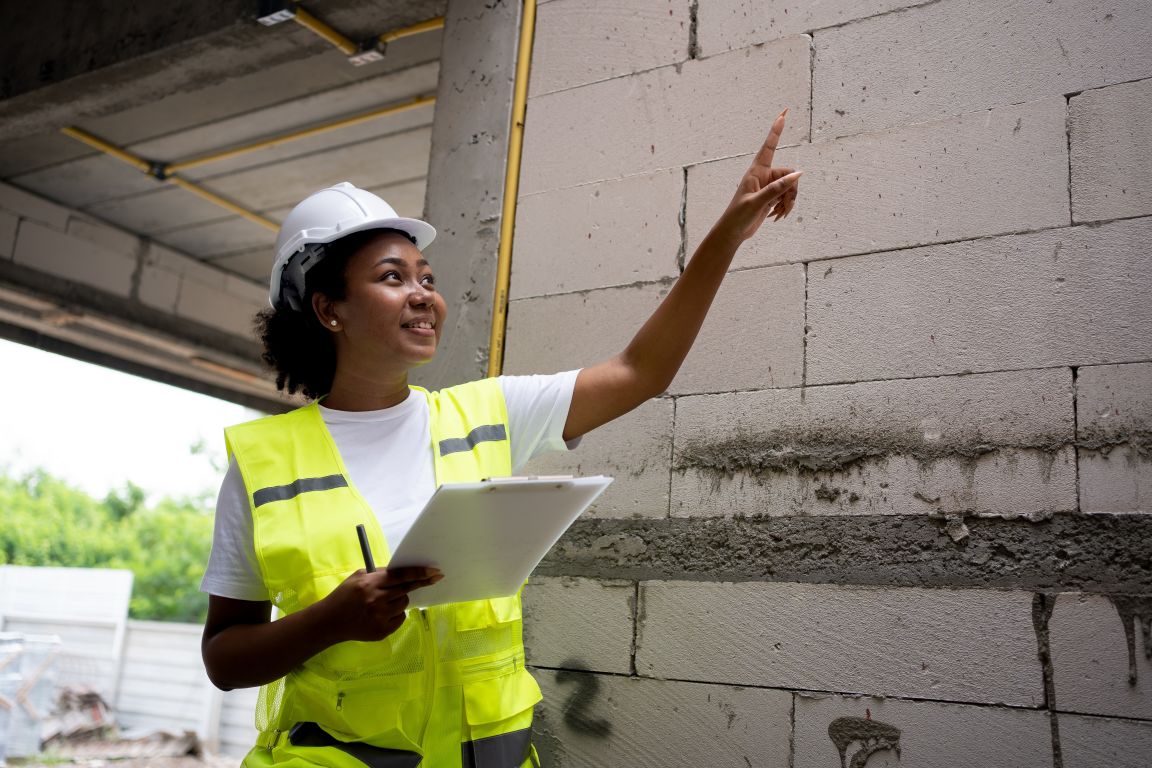
What an Industrial Hygienist Does for Facilities
An industrial hygienist identifies workplace risks and develops effective programs to eliminate those risks.
Industrial hygienists’ biggest value may come from prevention. Accidents that probably would have happened don’t happen when an industrial hygienist is on the job.
Some companies benefit from the paperwork, reports and plans industrial hygienists do because having them document, monitor and manage workplace risks helps ensure compliance with state and federal workplace safety laws.
An industrial hygienist also may help improve employee morale because employing a hygienist demonstrates a company’s commitment to safety.
What Does an Industrial Hygienist Do?
The word safety is vague enough to encompass almost everything. So how do industrial hygienists ensure worker and community safety? They use detailed, proven techniques on the job every day.
Identify
An industrial hygienist must be aware of all the dangers involved in a specific workplace, but they tend to focus on a few key issues such as:
Ergonomics: Are staff members supported while doing repetitive work like typing? Do they have assistance if they must stand all day? Are they required to lift and bend and, if so, can they do so safely? Anything involving a worker’s body falls into this category.
Noise: Some workplaces, such as mills or manufacturing plants, are inherently noisy, but an average office also could put workers at risk due to noise from construction or air-handling equipment. An industrial hygienist must understand what decibel levels are acceptable and what ones aren’t.
Temperature: Freezers and refrigerator trucks can cause workers significant harm, but so can hot kitchens and outdoor work. An industrial hygienist must understand the temperature ranges that keep workers safe.
Air quality: Solvents, paints, chemicals and other toxins can pollute the air workers breathe. Poor air handlers also can force workers to breathe stagnant air.
Exposure: Chemicals, radiation and biological hazards are present in multiple workplaces. Industrial hygienists work to limit those risks.
Create
With a list of both known hazards and new items that could pose a problem later, industrial hygienists develop risk mitigation plans that could involve the following elements:
Equipment: Do workers have everything they need to stay safe and comfortable? Could replacing outdated devices help?
Storage: Where should cleaning materials be housed? What about chemicals? How should purchases be logged and maintained?
Facilities: Is the space for workers up to date to help meet quality regulations?
Training: Does everyone understand the rules? Can the industrial hygienist spot violations?
Monitor
With rules in place, the industrial hygienist can schedule routine visits and inspections. Tests of temperature, air quality, noise and other key factors can ensure that mitigation programs are working properly.
Document
Industrial hygienists keep detailed records of their inspections, regulations and progress. If the company faces scrutiny, those documents could help prove the company is in compliance.
An industrial hygienist also maintains and updates material safety data sheets for every toxin within the organization. In case of a spill, these documents tell workers what to do next. Updating those documents and keeping them handy is a critical part of keeping workers safe.
Who Needs an Industrial Hygienist?
Workplaces that use chemicals obviously need a professional’s help. But industrial hygienists can be useful almost anywhere.
Industrial hygienists are often employed by the following organizations:
Agricultural companies.
Colleges and universities.
Government agencies.
Hazardous waste companies.
Hospitals.
Insurance companies.
Labor unions.
Manufacturing plants.
Public utility companies.
Research laboratories.
Tens of thousands of injuries happen in standard office spaces every year, but many could be prevented with some planning by an industrial hygienist.
Some organizations hire a full-time professional to assist with year-round safety and compliance, but other companies contract with service agencies. An industrial hygienist is assigned to the company, and that person tackles all the tasks required to keep workers safe. But the company isn’t required to take this person on as a permanent staff member.
Companies with many locations, large staffs and significant risks may save money by having a professional available around the clock. But smaller organizations may find the contract route more appealing and cost effective.
Alsco Helps Keep Workers Safe
Hiring an industrial hygienist to assess risks and write safety plans is a great way to reduce the risk of injury. But that’s just the starting point. You’ll need both safety equipment and supplies to help make your workplace safe.
When it comes to managing safety equipment and supplies, Alsco is the answer. With no up-front costs and no headaches, Alsco provides regular service and consistent resupply:
Easy to use and easy to manage cleaning chemicals.
Always-ready first aid, AED and eyewash cabinets.
Regularly cleaned floor mats and mops.
Disposable and reusable personal protective equipment.
Let Alsco design and supply an effective safety program for your employees. It’s easy to get started. Call us today to learn more.
References
You Need an Industrial Hygienist on Your Team (November 2021). Industrial Safety and Hygiene News.
Discover Industrial Hygiene. AIHA.
Industrial Hygiene: Keeping Workers Healthy and Safe (November 2015). Harvard T.H. Chan School of Public Health.
Five Common Office Hazards to Prevent. Society for Human Resource Management.